By Ben Hamlich, Director of Technical and Product Innovation, trueCABLE RCDD, FOI
What are fiber optic cables made of? Fiber optic cable It consists of five basic components: core, cladding, coating, reinforcing fibers, and cable jacket.
When looking for fiber optic cable, we need to pay attention not only to the connectors, such as SC to ST fiber cable, LC to SC Fiber Patch Cableor SC to SC patch cablebut also for the cable itself. There are also many different options available for fiber optic cables, such as LC to LC Multimode Duplex Fiber Optic Patch Cable and LC to LC Single Mode Fiber Optic Patch Cable.
What are the parts of a fiber optic cable?
In most cases, a fiber optic cable consists of five basic components: the core, which is responsible for transmitting the light signals; the sheath, which surrounds the core with a lower refractive index and contains the light; the coating, which protects the core; the fiber optic strength member; and the cable jacket. This article will provide a detailed introduction to the parts of a fiber optic cable. Watch the video below for more details!
What is the essence of optical fiber?
The core of a fiber optic cable is the physical glass medium that carries the optical signals from the attached light source to the receiver. Light is transmitted along the optical fiber through its smallest and most important component, called the core. The core of an optical fiber is most often made of glass, although some fibers are made of plastic as well. The glass used in the core is highly pure silicon dioxide (SiO2).2), a material so transparent that you will have the same experience looking through it from 5 miles away as if you were looking through a window in a house.
Depending on the intended use, fiber optic cores can be used in a variety of applications. The size of the core varies with the type of optical fiber. Typical glass core thicknesses can range anywhere from 8 to 10 micrometers for single mode and 62.5 to 50 micrometers for multi mode; these core sizes are the most common and widely used in the telecommunications industry.There are two basic categories of optical fibers: single-mode and multimode, which can be distinguished by the diameter of their cores. Light of a single wavelength travels toward the center of the core of a single-mode fiber, which has a core diameter of 8-10 microns, typically 9 microns for a single-mode fiber. Light in a multimode cable travels in multiple paths down the fiber and bounces between the core and the cladding as it travels down the core. The core of a multimode fiber can be either 50 microns (most common) or 62.5 microns in diameter.
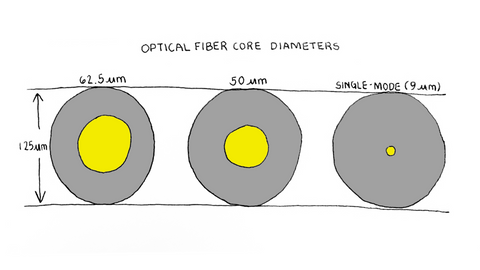
What is fiber optic cable sheath?
It is a thin layer that is pressed over the core and acts as a boundary that contains the light waves (more details on this later), allowing the data to travel along the length of the fiber.
The jacket is what surrounds the core of the optical fiber and has a lower refractive index than the core. This allows the optical fiber to work.
When using glass cladding, both the cladding and the core are produced simultaneously from a silicon dioxide based material in a permanently fused state. This process occurs when the glass cladding is applied.
During the manufacturing process, different amounts of catalysts are added to the core and cladding to keep the difference in refractive indices at about 1%. At a wavelength of 1300 nm, a typical core might have a refractive index of 1.49, while the cladding might have a refractive index of 1.47. On the other hand, these amounts change depending on the wavelength. At different wavelengths, the core of the same fiber will have a different refractive index than the rest of the fiber.
Cladding is also produced in conventional diameters throughout the manufacturing process. 125 µm and 140 µm are the two common sizes. A 125 µm cladding core typically ranges in size from 9 µm to 50 µm, and a 140 µm cladding core is 62.5 µm.
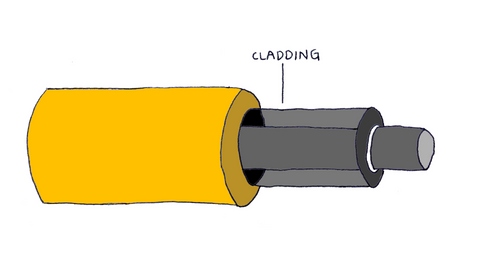
What is fiber optic coating?
The actual protective layer of the optical fiber is the coating. It prevents the sheath from being damaged by impacts, scratches, and even moisture by acting as a shock absorber. Without the coating, the optical fiber is highly susceptible to damage. Bending the optical fiber can create a single microscopic hole in the sheath, which can cause the fiber to break. Fiberglass of any type must be coated, and you will not be able to buy it without the coating. The ability of the optical fiber to transmit light is not affected in any way by the coating. In most cases, the outer diameter of the sheath is either 250 or 900 microns. In most cases, the coating is colorless. In some applications, it may be colored so that it can be easily identified.
A specific type of performance or environment led to the decision to use this particular coating. Acrylics are a very common form of coating. Typically, two coats of this coating are applied to the surface. The base coat is applied by rubbing it directly onto the cladding. This coating is gentle, and because of this, acts as a cushion for the optical fibers as they bend. The prime coat is somewhat softer than the secondary coat, resulting in a harder outer surface.
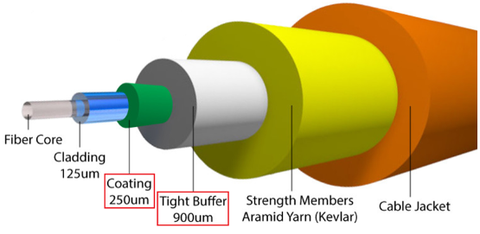
What are strengthening fibers?
Aramid yarns are used in fiber optic cables as a tensile strength component, meaning they help prevent the cable from stretching or breaking when subjected to tension. Additionally, they can be used to provide additional protection against crushing, bending, or twisting. Because they are flame retardant and self-extinguishing, aramid yarns can also be used as a fire protection component.
In the manufacture of fiber optic cables, aramid yarns are usually combined with other types of materials, such as a jacket material, which protects the cable from moisture and other environmental factors. In addition, a protective outer layer of steel or aluminum, which protects the cable from additional mechanical damage.
Aramid yarns are used in a variety of other applications in addition to their use in fiber optic cables. These other applications include cut-resistant clothing and bulletproof vests, as well as ropes and cables used in industrial and marine applications, and reinforcing composite materials used in the aerospace and automotive industries.
In fiber optic cables, aramid yarns play an important role as they protect the fragile optical fibers inside the cable from damage caused by mechanical stress.
As it provides mechanical and thermal protection to the optical fibers embedded within the fiber optic cable, aramid yarns play an important role in the overall process of ensuring reliable and safe operation of fiber optic cables.
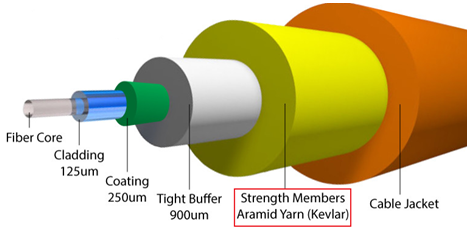
What is fiber optic cable sheath?
The protective coverings placed around fiber optic cables are very important in preventing the fragile fibers inside the cable from being damaged by external forces and elements. Below is a list of the different types of protective coverings that can be found on fiber optic cables:
Full session: Plenum rated jackets are made of fire resistant material and are used in air handling areas such as ceilings and walls.
The riser: High rating jackets are designed to be fire resistant and are used in vertical cable routes between floors. These lines are referred to as high jackets.
For Zaha: Smoke-free and halogen-free jackets are made of flame-resistant material and, when burned, produce very little smoke and no harmful halogen fumes.
outdoor: Jackets approved for use in outdoor environments are made to withstand harsh weather conditions, and protect against moisture and UV rays. Outdoor applications, such as buried or aerial cable lines, are among the most common places where you will find fiber optic cables installed. Outdoor cables typically have a PE cable jacket. Some of the PE options now in use are LLDPE (linear low-density polyethylene) and HDPE (high-density polyethylene).
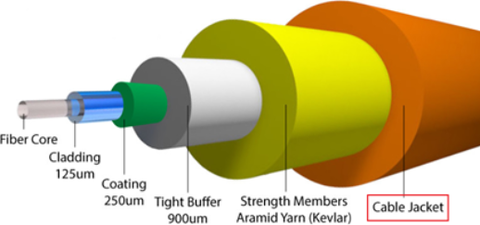
Environment, building codes and regulations may require a different type of jacket, each with a unique set of qualities and standards, and used in a distinct set of applications. It is best to check local codes to ensure you are using the correct cable jacket for your particular application.
Industry standards and best practices
To ensure that fiber optic cables perform at their best, industry standards have been developed. In the United States, TIA standards are used to ensure that all fiber optic cables follow the same performance specifications. In other parts of the world, such as Europe, ISO standards are the standards that must be followed for performance specifications. These standards set guidelines to ensure that light loss is within acceptable limits and that data transmission is maintained consistently and reliably. By following these best practices, technicians can avoid issues such as signal degradation and maintain the integrity of the communications network. These standards are designed to help everyone—from manufacturers to installers—achieve optimal results for their fiber optic cable installations.
Industry standards also help maintain consistency and reliability when manufacturing fiber optic cable, reducing the risk of failures before the cable is installed. When it comes to regulatory considerations, industry standards ensure that fiber cable is manufactured and tested according to a highly specific, relevant and up-to-date process.
Fiber Optic Cable Trends
Modern optical fibers evolve with developments that make cables thinner, more durable, and more reliable. For example, newer cables may use bend insensitive fibers Fiber optics are cables that can handle higher data rates and are easier to install, ensuring that fiber optics remains at the forefront of communications technology.
conclusion
In short, the core, cladding, coating, aramid yarn strength element, and cable jacket are the five components of an optical fiber found in a fiber optic cable. The coating protects the fiber from damage, the aramid yarn provides mechanical strength, and the cable jacket protects the fiber from the environment. The core is the central part of the fiber that carries the light signal. The jacket surrounds the core and reflects the light signal back to the core. The strength element, aramid yarn, provides mechanical strength. The coating protects the fiber from damage. These components, when combined, work together to ensure the efficiency and reliability of data transmission over long distances. It is impossible to overstate the importance of these fiber optic cable components, as they play a role in ensuring that modern fiber optic communications systems operate as intended.
Happy socializing!
trueCABLE provides the information on our website, including the Cable Academy blog and live chat support, as a service to our customers and other visitors to our website in accordance with our website. Terms and ConditionsAlthough the information contained on this site relates to data networks and electrical issues, it is not professional advice and reliance on such material is at your own risk.